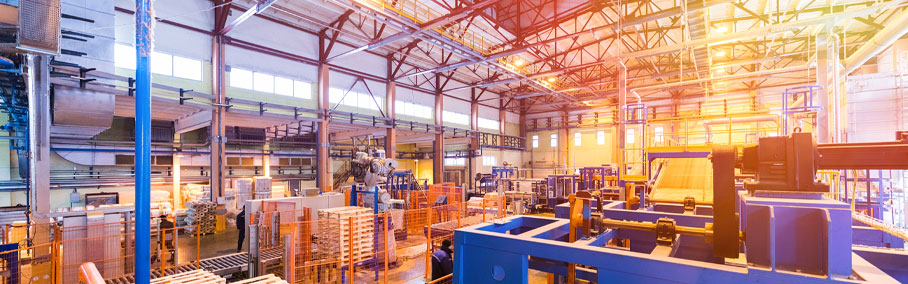
Manufacturing Process Methods Compared – When to Apply Master Schedule
We can generally sort Manufacturing Business processes into three groups: Make to Order, Assemble to Order, and Make to Stock. Make to Order is also known as custom build. Assemble to Order is used in repetitive manufacturing. And Make to Stock covers mass production of end products.
Let’s look at each one and see where to apply scheduling and planning tools for the best order to fulfillment timing.
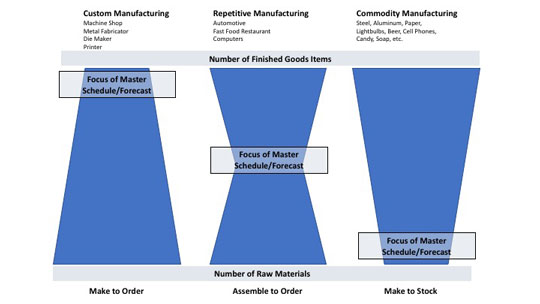
Make to Order
Make to Order is the manufacturing process in which a large group of components can be made into very specific end products.
A printer may carry stock of many types and grades of paper and have the ability to create thousands of Ink colors. Skilled workers can use the tools and materials to create any item a customer may want printed. Then they can mass produce that Item into as many copies as the customer would like.
A die maker has large billets of steel in stock and with tools and produces very detailed dies to the customer’s specifications.
A metal fabricator might carry a variety of sheet metal sizes and grades to custom build things like HVAC duct work or electronics cabinets or a drain pan for the local plumber.
Assemble to Order
Assemble to Order is the manufacturing process in which a large group of components can be made into a limited group of sub-assemblies to be kept in stock. The small number of sub-assemblies can then be grouped and assembled to create a large number of finished products. This can also be called “semi-custom” manufacturing.
An auto maker often sells a car based on various “option packages” that they offer. The customer may want to have a car model that has options like “sport package” or “luxury model” or “towing package”. The manufacturer may offer engine options, or a sunroof. The color can be chosen from a limited list of options for that year or model series.
Fast Food Restaurants carry ready-made or pre-cooked components which will then speed the final assembly or cooking time for quick delivery to the customer. Sandwich shops, hamburger places and taco eateries all base the quick service on the Assemble to Order model.
Computer manufactures offer to have you “Build your Own” computer on their website. They have you select the base computer you want and then a series of options will be presented as you make your selections. Some early choices may cause later options to be limited based on size and capacity constraints. The end result is a quick delivery of your “customized” computer. All of the sub-assemblies like the monitors, hard drives, cases, wiring harnesses, memory and mother boards are in stock and ready to assemble.
Make to Stock
Make to Stock is when a small group of components can be made into a larger group of finished goods. This method can be used for commodities and mass produced end products. Consumer electronics, cell phones, baby wipes, bathroom cleaner, children’s toys, candy, paper, steel, beer and the list goes on. The manufacturer wants to carry stock on the finished product so it can be quickly delivered to the distributor or end user.
A steel producer can take a few raw materials and produce a wide variety of steel grades in many shapes and sizes. Each grade and size is represented by a unique part number.
Light bulbs have a small list of components but can be built into many different end products. Shape, wattage, connection type all contribute to the variety of part numbers that can be sold.
Candy has very few ingredients such as sugar, milk, salt, flavorings and colors, but can be made into a wide variety of end products.
Basic Soap only has four ingredients: oil, potassium hydroxide, water, and fragrance (optional). Make just a few changes and you can produce multiple varieties of soap.
Applying the Master Schedule to the Manufacturing Process
The key Difference in the planning process for each of these manufacturing philosophies can be made on where the Master Schedule/Forecast is applied. Where can we make the best prediction on sales and have the shortest time from Order to Fulfillment?
Make to Order doesn’t provide any insight to planning what end items need to be built since the customer has not ordered from us yet. We can make some reasonable predictions on what we have built in the past and the kind of products a customer might ask for. The printer will carry a variety of paper and ink that will work on the kind of presses he has in his plant. We will need to determine things like what are the most common things we normally print: Documents or photo brochures? Where is our business located? If we are in Columbus, Ohio we will need lots of red and grey ink. If we are in Ann Arbor, Michigan we better carry a lot of blue and yellow ink. Regardless of our best forecasting, those manufacturers who use the Make to Order methodology should apply Master Schedule at the component level.
Assemble to Order should apply Master Schedule at the sub-assembly level. What groups of options are the most popular? What have we sold in the past? We want to be ready to fill orders quickly.
Make to Stock should apply Master Schedule at the finished goods level. If we have some input or forecast numbers from our customers we can incorporate them into our Master Schedule and hopefully make reasonable predictions.
Continue to follow the next blog in my series examining Material Requirements Planning. Next month: MRP — Opening the Black Box. Read our past blog “A Brief History of MRP – Materials Requirements Planning” Also, you can register for our upcoming webinar Master Scheduling and MRP… Stuff You Never Dreamed Of.