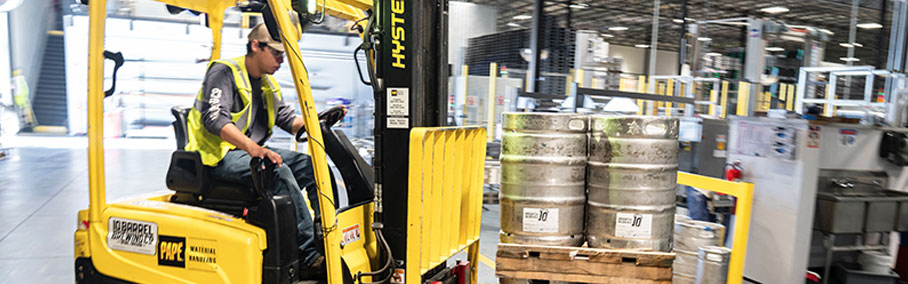
The Value of Inventory Traceability
As an ERP and business consultant, I am often asked about the value of and need for inventory traceability. Inventory traceability is the ability to trace products and materials through the supply chain. For manufacturers, this feature is of particular concern. Manufacturers need the ability to trace the components and materials used in their finish products back to the source from which they came.
The Cost of Inventory Traceability
Inventory traceability is often based on lots divided by a common attribute: manufacture date, supplier batch, material batch serialized containers, and/or serialized individual products. Serious discipline and (often manual) effort are required to implement such lot traceability. That effort drives up the need for manpower and increases labor costs. It is that cost that often causes management to question the value of inventory traceability. Organizations ask whether the processes around maintaining inventory traceability are something for which their customers are willing to pay. While customers do not always explicitly state it, the overwhelming evidence is that inventory traceability is an ever-increasing requirement in many industries and that it is becoming an expectation of suppliers.
The Value of Inventory Traceability
News stories of product recalls — ranging from automotive airbags to packaged lettuce – highlight the need for manufacturers to respond quickly to consumer issues, especially where safety is involved. In such situations, if a company hopes to minimize product liability and protect their brand, they must act immediately to identify and quarantine defective products. When issues result from supplier products, these same companies expect their suppliers to respond immediately with information to assist them in identification and mitigation activities. It is through inventory traceability that these expectations can be met.
Evolution of Inventory Traceability Technology
In the past, inventory traceability in manufacturing entailed manually recording material lot depletion on paper container tags and storing those documents for retrieval. Such methods provided slow and inaccurate information in times of downstream defect occurrence. Modern systems support these requirements through enhanced and integrated barcoding, scanning and software. RFID utilization continues to grow and the best ERP solutions support inventory management at the container or individual level. Through the benefits of such technology, the cost of inventory traceability continues to decrease while time to trace dramatically improves. The technology investment pays for itself by providing more accurate information and improved inventory turnover rates.
The Demand for Inventory Accuracy
The demand for inventory accuracy is more important now than ever before. Consider the risk of losing customers who are demanding enhanced traceability. In a recent statement, Walmart has announced that some suppliers have twelve months to adopt IBM blockchain platform for traceability. CNBC reports that Walmart is expecting some produce suppliers to “enable end-to-end traceability” back to farms “in seconds – not days”.
An ERP system with good inventory traceability capabilities can arm you with the tools you need to meet the expectations of your customers and suppliers. Revolution Group helps manufacturers gain insight into their businesses through integrated ERP solutions. If you would like to learn how Revolution Group can help you reach your business goals, give us a call at 614-212-1101 or email us at [email protected]. We would love to change the way you think about ERP.